自动化项目逐步向数字化方向转变
工业自动化的发展正在经历一场变革,传统的工业自动化在新的IT技术的推动下,正在探索新的发展方向,而对于这个新的方向,目前西门子给出的答案是数字化。
按照之前的理解,数字化是传统的工业自动化向着满足快速、高效、节能的生产控制系统发展的一个目标。具体实现的方式是通过数字化的软件,将原来自动化产线制造、集成、生产的实际过程变成虚拟的过程,通过虚拟调试,使得未来的产线能够以“虚拟现实”的方式呈现在人们面前。这种方式甚至可以实现整条产线、整个工厂的生产过程的模拟,大大节省了企业前期调试的成本。同时,这种方式还能模拟生产过程中可能出现的各种情况,使人们在实际产线或者设备在真正的被制造之前,就已经对设备的各种动作有了全面的测试和了解。
但这种方式是否能够真正满足未来自动化生产的需要?是否能真正带来益处?这是否是真正可以实现的目标,这个目标什么时候可以实现?
这里,我介绍几个小的应用实例,供大家探讨。
虚拟调试
西门子为用户设计制造一个设备Demo,该设备Demo机械部分包括传送带、机械手臂(图1)。
图1 设备Demo
在整个Demo设计的过程中,采用了虚拟调试的方法。
首先,除了机械部分的设计外,设备动作设计采用了NX MCD软件,对整个设备的动作和工艺进行了模拟仿真,发现其中的错误可以及时改正。
接下来,对于控制器系统的设计和调试,均采用PLC SIM Advance软件进行模拟调试(图2)。
图2 PLCSIM Advance 仿真程序
此时,可以通过软件对PLC控制程序以及画面进行调试。这里的仿真软件可以代替真实的PLC硬件,可以在没有PLC硬件的情况下,随时随地的进行程序的仿真调试。
同时,还可以将该PLC程序仿真与MCD仿真进行连接,通过PLC程序来控制MCD中设备的动作(图3)。
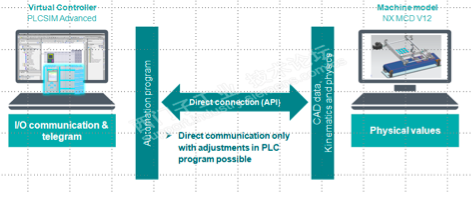
图3 PLC仿真程序与MCD仿真程序互连
通过这样的关联,几乎可以对设备进行实际的调试了,只不过整个过程都是在软件环境下实现的,但效果跟实际的设备几乎完全一样。
由于采用了虚拟调试的方法,在机械部件被设计出来之后,在制造的过程中,整个设备的控制程序就已经可以进行编制和调试了。而且,无论是机械部分还是程序部分,都大大减少了实际设备的错误率。根据我们同事的介绍,他们整个项目的设计过程(包括机械硬件、软件程序)大概持续了半年,但在现场进行设备零部件组装以及程序调试的时间总共花了2周左右,这其中还包括了机器手臂的调试。
数字化Pump App on MindSphere
现场正常工作的设备,可以通过特定数据的采集,对设备的运行状态进行评估,对可能出现的故障进行提前预判,从而避免事故的发生,防止出现更严重的损坏或者损失。
这里举个对现场的Pump进行预维护的一个应用实例(图4)。
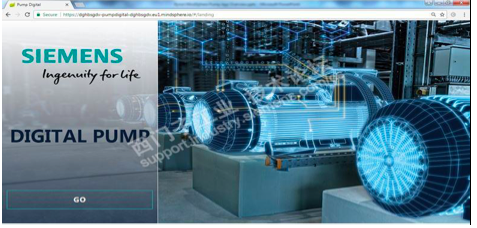
图4 Digital Pump App
通过相应的数据采集,可以对现场设备的运行状态、效率等参数进行详尽的记录和分析,而访问这些数据,则是通过Web的方式即可(图5)。
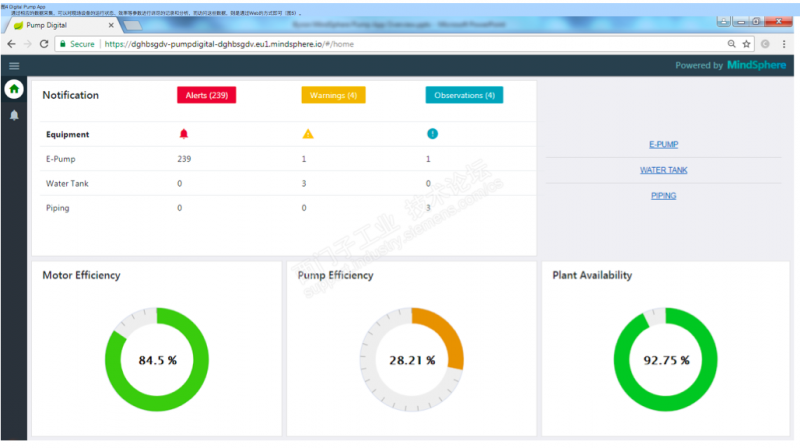
图5 现场数据分析结果
考虑到设备可能位于不同地点,甚至遍布全球,另外,考虑到数据的存储方便,这里将采集到的数据通过PLC上传至西门子MindSphere云端。
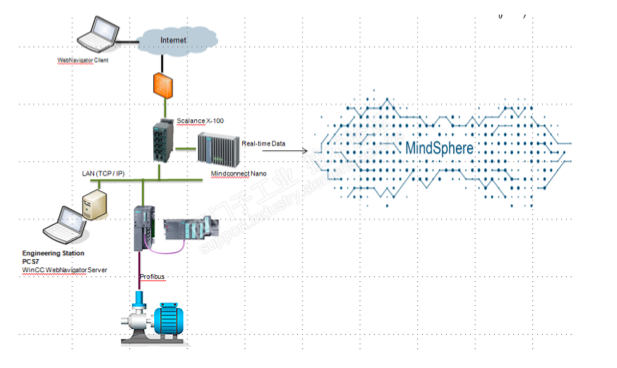
图6 PLC数据上传至云端
而最近,西门子已经与阿里云达成协议,未来将MindSphere部署于阿里云,为广大国内用户提供基于云端的应用服务。
通过这两个小的应用实例,大家是否已经感受到数字化的脚步在慢慢临近,是否体会到工业自动化的数字化变革所带来的变化?而这些变化将会如何引导工业自动化发展的方向,最终如何实现智能化制造?可以谈谈您的看法!